Molded grilles, also known as molded grating or molded fiberglass grating, are robust, corrosion-resistant panels commonly used in industries such as marine, chemical processing, oil and gas, wastewater treatment, and infrastructure. These grilles are manufactured using a combination of thermoset resin systems and fiberglass reinforcements through a process known as molding or compression molding. The manufacturing of these products requires a specialized set of machinery and equipment that ensures strength, uniformity, and precision in the final product.
Einführung zur Produktleistung
This article provides a detailed and technical introduction to molded grille machinery and equipment, covering the manufacturing process, machine components, operational workflows, automation systems, safety features, and emerging industry innovations.
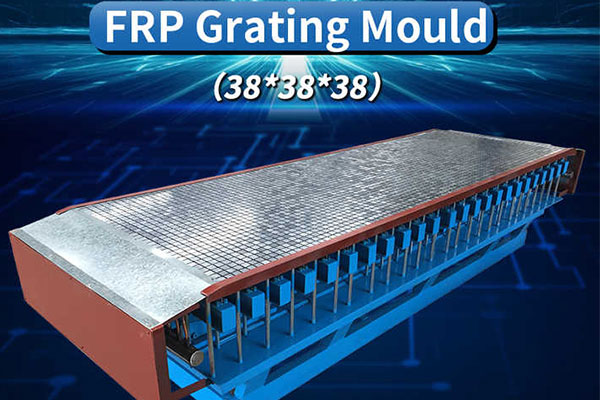
fiberglass Molded grille machinery and equipment
2. Overview of Molded Grilles
Molded grilles are typically produced from reinforced plastic composites. The manufacturing process involves laying fiberglass strand matting in a mold, followed by the addition of resin, which is then cured to form a strong, rigid, and corrosion-resistant product.
2.1 Key Characteristics
-
Corrosion resistance
-
Slip resistance
-
Electrical insulation
-
Non-magnetic
-
Hohes Verhältnis von Festigkeit zu Gewicht
2.2 Applications
-
Industrial platforms and walkways
-
Drainage trench covers
-
Cooling tower floors
-
Offshore installations
-
Architectural facades
-
Food and beverage plants
3. Molded Grille Manufacturing Process
3.1 Pre-Molding Preparations
-
Mold cleaning and release agent application
-
Preparation of fiberglass mat (chopped strand mat or continuous roving)
-
Pre-mixing of resin systems (polyester, vinyl ester, phenolic, etc.)
3.2 Molding Process
-
Fiberglass Lay-up: Layers of fiberglass are laid manually or automatically into the mold.
-
Resin Pouring: Thermosetting resin is poured evenly over the fiberglass.
-
Curing and Heating: The mold is subjected to controlled heating (50–130°C) to initiate curing.
-
Cooling and Demolding: After curing, the mold is cooled and the molded grille is demolded.
-
Trimming and Surface Finishing: The panel edges are cut and surface finish is applied if necessary.
3.3 Post-Processing
-
Grinding or sanding edges
-
Drilling or slotting
-
Painting or surface treatment (anti-slip coatings)
4. Molded Grille Machinery and Equipment
The equipment used in molded grille manufacturing can be divided into core molding machinery, ancillary equipment, Und automation systems.
4.1 Core Molding Equipment
4.1.1 Mold Presses (Hydraulic or Pneumatic Presses)
These are heavy-duty press machines capable of delivering up to 1500 tons of pressure. The press ensures the resin impregnates the fiberglass uniformly under heat and pressure.
Hauptmerkmale:
-
Plate size: Custom sizes from 1.2m x 2.4m to 1.5m x 3.6m
-
Heated platens: Integrated with electric or oil-based heating elements
-
Programmable logic controls (PLC) for curing cycle
-
Safety interlocks to prevent accidents
4.1.2 Mold Sets
Reusable steel or aluminum molds with grid-shaped cavities form the structure of the grille.
Typen:
-
Square or rectangular mesh
-
I-bar or T-bar styles
-
Custom depth (e.g., 25mm, 38mm, 50mm)
4.1.3 Resin Dispensing System
Precision metering systems ensure the accurate mix and delivery of resin components.
Merkmale:
-
Automatic metering pumps for resin/hardener
-
Static or dynamic mixing heads
-
Programmable flow rate control
-
Vacuum degassing system (optional)
4.2 Auxiliary Equipment
4.2.1 Fiberglass Chopper
Cuts continuous roving into short lengths (25–50 mm) used in the lay-up process.
4.2.2 Heating System
-
Electric heaters or thermal oil heaters
-
Maintain consistent mold temperature
-
Integrated with temperature sensors and feedback loops
4.2.3 Cooling System
-
Water-cooling or air fans to bring down mold temperature post-curing
-
Reduces cycle time
4.2.4 Mold Release Systems
-
Spray units for even application of mold release agents
-
Silicone or wax-based
4.2.5 Demolding Equipment
Hydraulic or manual systems used to lift and release the finished grating from the mold.
4.2.6 Edge Trimmers and Grinders
Post-processing machines to smooth and trim panel edges to precise dimensions.
4.3 Automation and Digital Systems
Modern production lines are incorporating more automation for efficiency and quality control.
4.3.1 PLC-Controlled Systems
Automated resin flow, heating/cooling cycles, and curing times for repeatable results.
4.3.2 SCADA Integration
Supervisory control and data acquisition systems to monitor all machine parameters and provide remote diagnostics.
4.3.3 Robotic Resin Dispensers
Robots equipped with flexible nozzles for accurate resin laying.
4.3.4 Automatic Panel Pickers
Gripping systems to pick, stack, and move molded panels to storage or further processing lines.
5. Materials and Compatibility
5.1 Fiberglass Reinforcements
-
E-glass or S-glass roving
-
Chopped strand mat (CSM)
-
Woven roving
-
Pulled or cut fibers depending on application
5.2 Resin Systems
-
Unsaturated Polyester Resin (UPR): Standard, economical
-
Vinylesterharz: For chemical resistance
-
Phenolharz: Flame-retardant applications
-
Epoxidharz: High-performance composite gratings
5.3 Additives
-
Pigments
-
Fire retardants
-
UV stabilizers
-
Anti-slip fillers
The machinery must support uniform dispersion and compatibility with these materials.
6. Plant Layout and Production Workflow
6.1 Typical Layout
-
Material storage area (resin, fiberglass)
-
Cutting/Chopping zone
-
Lay-up and molding line
-
Curing ovens (if separate from press)
-
Demolding and post-processing zone
-
Quality control lab
-
Packing and warehouse
6.2 Workflow Steps
-
Raw material check-in
-
Fiberglass cutting and preparation
-
Lay-up in mold
-
Resin mixing and dispensing
-
Compression molding
-
Curing, cooling, and demolding
-
Edge trimming and inspection
-
Packing and dispatch
7. Safety and Environmental Control
7.1 Safety Features
-
Emergency stop systems on all presses
-
Safety enclosures around moving parts
-
Heat shielding around hot components
-
Interlocked doors during molding operation
-
Overpressure protection valves
7.2 Environmental Controls
-
VOC extractors for resin fumes
-
Dust collection units in grinding zones
-
Resin spill containment systems
-
PPE and ventilation systems
8. Industry Standards and Quality Assurance
8.1 Standards
-
ANSI/ACMA FGMC Standards
-
ISO 9001:2015
-
ASTM D635 (Flammability)
-
EN ISO 14122-2 (Industrial floor grating)
8.2 Quality Checks
-
Load-bearing tests
-
Resin-to-glass ratio inspection
-
Dimensional tolerance measurement
-
Color and surface finish comparison
-
Fire-retardant testing
9. Maintenance and Lifecycle Management
9.1 Regular Maintenance Tasks
-
Check hydraulic fluid levels and pressure
-
Inspect press alignment and platens
-
Clean mold surfaces and reapply release agent
-
Calibrate resin flow meters
-
Replace filters and temperature sensors
9.2 Predictive Maintenance
-
Vibration analysis
-
Thermal imaging for heater health
-
SCADA analytics for performance trends
Proper maintenance extends machinery life and ensures consistent product quality.
10. Key Global Manufacturers of Molded Grille Machinery
-
YUSHENG FRP Machinery (China)
-
Jiangsu Jinlong FRP Equipment
-
Huayang FRP Mould Co., Ltd.
-
Glasteel Industrial Equipment (Mexico)
-
Polser Composite Machinery (Turkey)
-
Pultrall Inc. (Canada) – for mold and post-processing equipment
-
Custom Equipment from OEM builders (USA, EU)
Many companies customize press lines and mold sizes based on client product specs.
11. Innovations and Future Trends
11.1 Smart Factories
-
Real-time monitoring
-
Predictive analytics
-
Robotic grating inspection
11.2 Eco-Friendly Manufacturing
-
Low-VOC resins
-
Closed-loop resin systems
-
Biocomposite grating (e.g., with natural fibers)
11.3 High-Precision Mold Design
-
CNC-machined molds for tighter tolerances
-
3D-printed tooling for prototypes
11.4 Modular Production Cells
-
Flexible, scalable cells for batch production
-
Plug-and-play automation units
12. Conclusion
Molded grille production is a technologically sophisticated process that requires precise control over temperature, pressure, resin flow, and fiber orientation. The machinery involved—from massive hydraulic presses to automated resin dispensers and robotic pickers—must function seamlessly to ensure high product quality and efficient production.
Investing in high-quality molded grille machinery not only boosts manufacturing capabilities but also opens the door to innovation in product design and performance. As industries increasingly demand lightweight, corrosion-resistant, and low-maintenance materials, the role of molded grating and its production technology will continue to expand.
Molded grille machinery and equipment
Serie :
supporting equipment >Anwendung
Industrial platforms and walkways Drainage trench covers Cooling tower floors Offshore installations Architectural facades Food and beverage plants
Markenname :
TF-Verbundwerkstoff
Produktname :
Molded Grille Machinery
FAQ
Q :
How is molded grating different from pultruded grating?
A :
Molded grating is made by pouring resin over fiberglass mats in a mold, resulting in a bidirectional strength pattern. Pultruded grating is made by pulling continuous fiberglass strands through a resin bath and a heated die, offering higher longitudinal strength.
Q :
What type of press is used in molded grille production?
A :
A hydraulic compression press with heated platens is most commonly used. Press capacity ranges from 500 to 1500 tons, depending on the grille size and thickness.
Q :
What materials can the machinery handle?
A :
The machinery is compatible with: Fiberglass (E-glass or S-glass) Resins (polyester, vinyl ester, epoxy, phenolic) Additives like UV inhibitors, pigments, and flame retardants
Q :
How are molds designed for different grille sizes?
A :
Molds are custom-fabricated based on required: Mesh patterns (square, rectangular) Panel thickness (e.g., 25 mm, 38 mm, 50 mm) Grille surface type (concave, gritted, plain)
Q :
What’s the typical cycle time for one molded grille panel?
A :
The complete cycle—from lay-up to demolding—usually takes 30–90 minutes, depending on panel size, resin type, and curing system.
Andere verwandte Produkte