New change Jiangxi Tianfu fiberglass grating factory
Fiberglass Reinforced Plastic (FRP) grating is produced using a specialized process involving the pouring of resin and the embedding of fiberglass reinforcement into molds. This process results in a strong, durable, and corrosion-resistant product. The pouring and molding area refers to the section of the production facility where the resin is mixed, poured, and cured to create the FRP grating.
Below is a detailed explanation of the FRP grating pouring and molding area, including key considerations, processes, and equipment used.
1. Key Components of the FRP Grating Pouring and Molding Area
a. Mixing and Pouring Station
- Resin and Hardener Mixing: A critical part of the process involves mixing the resin (usually unsaturated polyester or vinyl ester) with a hardener or catalyst to initiate the curing process.
- Reinforcement Materials: The fiberglass reinforcement, often in the form of mats, roving, or woven fabrics, is cut to size and prepared for placement into molds.
- Resin Pouring: The mixed resin is poured over the fiberglass reinforcement to saturate and bond it thoroughly. This is usually done in a controlled environment to maintain consistency and quality.
b. Molding Area
- Mold Preparation: Molds are prepared to the correct size and shape for the desired grating panel. They are often made of steel, aluminum, or other rigid materials.
- Gel-Coating (Optional): For additional protection and aesthetic purposes, a gel-coat layer is applied to the inside of the mold to improve surface quality and enhance corrosion resistance.
- Lay-Up Process: Fiberglass layers (mats, roving, etc.) are laid into the mold and saturated with resin. The fiberglass reinforcement is typically arranged in multiple layers to ensure strength.
- Compression and Compaction: Some FRP grating products undergo a compression process where the fiberglass-resin mixture is compacted to remove air bubbles and ensure uniform thickness.
c. Curing Station
- Curing Process: Once the resin is poured and the fiberglass is properly arranged, the grating is left to cure. The curing time depends on the type of resin, the thickness of the grating, and the ambient temperature. Curing can take place at room temperature or may be accelerated using heat (oven curing).
- Post-Curing: After the initial curing phase, FRP grating may undergo a post-curing process to further harden and improve its mechanical properties.
d. Demolding
- Mold Removal: Once the grating has fully cured, it is carefully removed from the mold. This step may involve the use of release agents to ensure that the grating does not stick to the mold.
- Edge Trimming: After removal, any excess material or sharp edges are trimmed and finished to meet the required dimensions.
2. Equipment in the Pouring and Molding Area
a. Mixing Equipment
- Resin Mixing Tanks: Large tanks equipped with mechanical stirrers to ensure the resin and hardener are mixed thoroughly.
- Metering Pumps: Used to ensure accurate quantities of resin and hardener are used in the mixture.
- Pigment Dispensers: Sometimes added to the resin mix for coloring purposes.
b. Molds
- Steel/Aluminum Molds: Molds are designed to form the grating panels to the exact specifications, including thickness and surface pattern.
- Gel-Coating Equipment: Equipment to apply a gel coat to the inside of the mold for surface protection and finish.
c. Curing and Heating Equipment
- Curing Ovens: In some cases, ovens are used to accelerate the curing process and improve the quality of the finished grating.
- Curing Racks: Racks are used for placing the molded grating for natural curing, typically in a controlled temperature and humidity environment.
d. Post-Molding Finishing
- Cutting and Trimming Tools: Once the grating has cured and been removed from the mold, excess material and edges are trimmed using cutting tools like saws or routers.
- Polishing/Grinding Equipment: After trimming, the surface of the grating may be polished or smoothed for aesthetics and to remove any rough spots.
- Quality Inspection Tools: Inspection tools such as calipers and micrometers are used to ensure the dimensions and quality of the molded grating meet specifications.
3. Considerations for FRP Grating Molding Process
a. Material Selection
- The type of resin (e.g., polyester, vinyl ester, or epoxy) significantly influences the strength, corrosion resistance, and curing time of the grating. The fiberglass reinforcement must be compatible with the resin to provide the required mechanical properties.
- The thickness of the grating, type of reinforcement (unidirectional vs. woven), and grid pattern must be considered to ensure the final product meets load-bearing and durability requirements.
b. Environmental Conditions
- Temperature and humidity play a critical role in the curing process. High humidity can interfere with the curing of the resin, while extreme temperatures can cause the resin to cure too quickly or unevenly.
- It is essential to control the environment in the pouring and molding area to maintain the integrity of the final product.
c. Curing Time
- Curing time must be carefully controlled. While ambient temperature curing is possible, accelerated curing using ovens or heat lamps can speed up the production process. However, fast curing may reduce the mechanical properties if not done correctly.
d. Health and Safety
- Ventilation: The pouring and molding area must be well-ventilated to avoid inhaling fumes from the resin or hardener, which may be harmful.
- Protective Equipment: Workers must wear protective gloves, goggles, and respirators when handling resins and fiberglass to avoid skin irritation and inhalation of harmful particles or fumes.
- Storage: Proper storage of raw materials such as resin, hardeners, and fiberglass is necessary to maintain their quality and prevent contamination.
4. Quality Control and Inspection
- Visual Inspection: After curing and demolding, the grating is visually inspected for defects such as air bubbles, uneven resin distribution, or imperfections in the surface.
- Dimensional Inspection: The final product is measured for correct dimensions and tolerances, ensuring it fits within the desired mold size and meets specifications.
- Strength Testing: Samples may undergo tensile, bending, or impact testing to ensure the FRP grating meets the necessary load-bearing and performance standards.
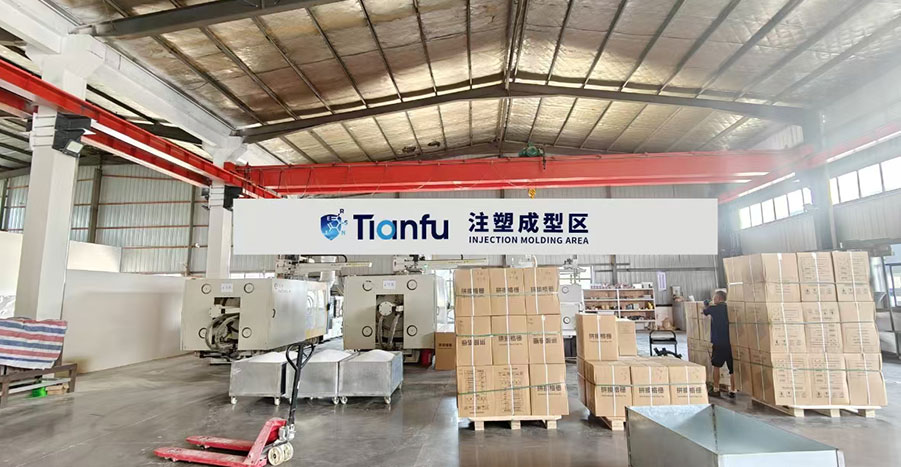
Fiberglass reinforced plastic grating factory
The Injection Molding Area refers to the section of a manufacturing facility where the process of injection molding takes place. Injection molding is a widely used manufacturing technique to produce parts by injecting molten material (such as plastic, metal, or other polymers) into a mold. This process is particularly suitable for mass production of parts with complex geometries and high precision.
In the context of Fiberglass Reinforced Plastic (FRP) or similar materials, the injection molding process can involve injecting a resin mixture (often with glass fibers or other reinforcements) into a mold to create a solid, reinforced plastic part. The Injection Molding Area is critical for ensuring the quality and consistency of parts produced through this method.
Below is a comprehensive breakdown of the Injection Molding Area for typical plastic injection molding, which can be adapted for FRP or other composite materials.
1. Key Components of the Injection Molding Area
a. Injection Molding Machine
-
Machine Overview: The injection molding machine is the core piece of equipment used in this process. It consists of three main sections:
- Injection Unit: This is where the material (plastic or composite) is heated to its molten form and injected into the mold cavity.
- Clamping Unit: This section holds the mold in place during the injection and cooling process.
- Mold: The mold cavity is the custom shape that the molten material is injected into. It gives the part its final shape once the material cools and solidifies.
-
Types of Injection Molding Machines:
- Hydraulic Machines: Common for general molding applications.
- Electric Machines: Provide higher precision and efficiency.
- Hybrid Machines: Combines the advantages of both hydraulic and electric systems.
b. Material Preparation Area
- Resin Handling: In the case of composite or FRP injection molding, the base resin (such as polyester or vinyl ester) is mixed with reinforcements like fiberglass, fillers, or additives.
- Pelletizing: For traditional plastic injection molding, materials are often in the form of pellets, which are stored in hoppers before being fed into the injection machine.
- Drying Systems: Many resins (especially composites) require drying before injection to prevent moisture contamination, which can degrade the quality of the molded part.
c. Injection Mold
- Mold Design: The mold is a hollow cavity that determines the final shape of the product. It is made from durable materials such as steel or aluminum and is precisely engineered to meet the design specifications of the product.
- Cooling Channels: Molds contain cooling channels through which a cooling fluid (usually water) circulates to rapidly cool the molten material and speed up cycle times.
- Ejection System: After cooling, an ejection system is used to remove the molded part from the mold cavity. This could involve pins, plates, or other mechanical methods.
d. Auxiliary Equipment
- Chillers: Chillers are used to regulate the temperature of molds and machines, ensuring proper cooling during the injection cycle.
- Granulators/Grinders: If recycled material or waste parts are being reused, granulators are used to break down the material into smaller pellets before being reintroduced into the molding process.
- Coloring Units: For plastic molding, colorants are sometimes injected into the resin, requiring a specialized unit for precise control of color quality.
2. Injection Molding Process for FRP (Fiberglass Reinforced Plastic)
While traditional injection molding uses pure plastics, FRP Injection Molding involves incorporating fiberglass or other reinforcement fibers into the process to enhance mechanical properties. Here’s how the injection molding process typically works for FRP:
a. Resin and Fiber Preparation
- Resin: The resin, which could be polyester, vinyl ester, or epoxy, is mixed with hardeners and catalysts (depending on the type of resin used). In some cases, colorants, flame retardants, or other additives are added.
- Fiberglass: Fiberglass reinforcement is often supplied in chopped strands, mats, or rovings. In injection molding, chopped strand mat is typically used, but continuous fibers may also be integrated, depending on the strength requirements of the final part.
b. Loading the Injection Molding Machine
- Material Loading: The resin and fiberglass mixture (in the case of chopped strand mats, it is pre-formed) is loaded into a hopper connected to the injection molding machine. The machine’s feeder system then transports the material into the heated barrel.
- Preheating (if necessary): Some composite resins may need to be preheated to ensure proper flow and bonding with the fiberglass reinforcement.
c. Injection Process
- Melting and Mixing: In the injection unit, the resin is melted to a molten state, and the fiberglass is blended with the resin. The mixture is homogenized to ensure uniform distribution of the fibers throughout the resin.
- Injection: The molten resin-fiberglass mixture is injected into the mold under high pressure. The pressure ensures that the material fills the mold cavity and conforms to its shape.
d. Cooling
- After injection, the mold is cooled using water or another cooling medium. The cooling time depends on factors like the material, part thickness, and mold design.
- Mold Ejection: Once the material has cooled and solidified, the mold is opened, and the molded part is ejected.
e. Post-Processing
- Trimming: The molded part is often trimmed or finished to remove any excess material (like flash or runners).
- Curing: Some FRP parts may undergo post-curing at elevated temperatures to improve their mechanical properties.
3. Considerations for the Injection Molding Area
a. Material Selection
- Choosing the right resin and fiberglass reinforcement is crucial to achieve the desired properties (strength, corrosion resistance, UV stability, etc.) for the final product.
- The type of resin used affects curing times, mold temperatures, and cycle times, all of which influence production efficiency and cost.
b. Mold Design
- Complexity: Injection molds can be complex and expensive to design and produce. The mold design must ensure efficient flow of the molten resin and fiberglass, with appropriate gating systems, vents, and cooling channels.
- Surface Finish: The mold’s surface finish will affect the final part's appearance. This can be influenced by the choice of mold materials and post-molding treatments.
c. Process Control and Monitoring
- Temperature Control: Maintaining optimal temperatures in the injection machine and mold is critical for ensuring quality. Too high or too low temperatures can result in defects like incomplete filling or warping.
- Pressure and Flow Control: Monitoring pressure and flow rates ensures that the mold is filled uniformly and completely, preventing defects.
- Cycle Time Optimization: Reducing cycle times can increase throughput and reduce costs, but this must be balanced with the need for proper cooling and material solidification.
d. Environmental Conditions
- Ventilation: Proper ventilation is essential, especially if working with resin systems that release volatile organic compounds (VOCs) or other fumes during curing.
- Humidity and Dust Control: Humidity can affect resin curing, and dust or contamination can negatively affect the surface quality of the molded parts.
4. Safety and Maintenance in the Injection Molding Area
- Protective Equipment: Operators must wear appropriate personal protective equipment (PPE), including gloves, goggles, and respirators, especially when handling resins, fiberglass, and other chemicals.
- Safety Protocols: Fire safety protocols are important due to the potential flammability of resins and fiberglass. Proper storage of raw materials and chemicals is essential.
- Maintenance: Regular maintenance of injection molding machines, molds, and auxiliary equipment is necessary to prevent breakdowns, ensure efficiency, and maintain product quality.
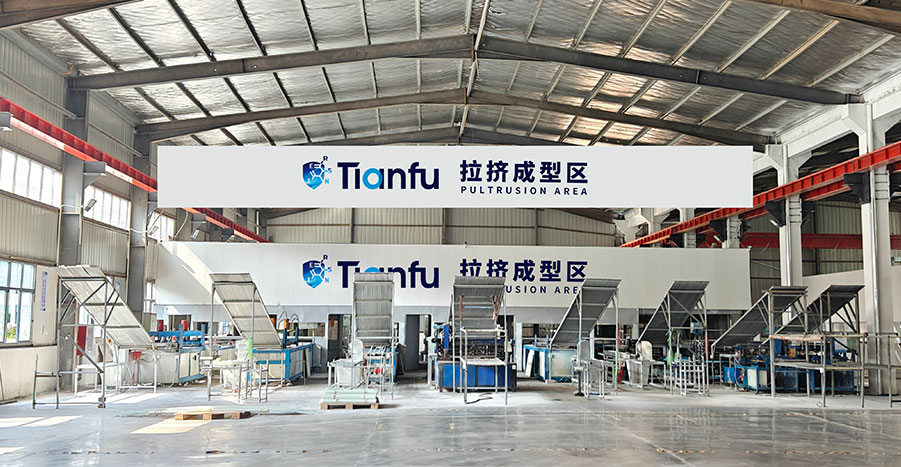
Fiberglass reinforced plastic grating factory
The Pultrusion Molding Area refers to the section of a manufacturing facility where pultrusion molding takes place. Pultrusion is a continuous process used to manufacture composite materials, specifically fiberglass reinforced plastics (FRP). In this process, continuous fibers (usually fiberglass) are pulled through a resin bath, then shaped and cured in a heated die to form long, rigid profiles like beams, rods, angles, or channels.
The pultrusion molding area is key to ensuring that pultruded composite parts meet design specifications for strength, durability, and performance in various applications such as construction, infrastructure, automotive, and aerospace.
Below is a detailed breakdown of the Pultrusion Molding Area, including key processes, equipment, and considerations.
1. Key Components of the Pultrusion Molding Area
a. Pultrusion Machine
The pultrusion machine is the core piece of equipment in the molding area. It consists of several components that work together to shape and cure the composite part:
- Resin Bath: The continuous fiberglass reinforcements (fibers, mats, or rovings) are impregnated with resin in this bath. The resin is typically polyester, vinyl ester, or epoxy, depending on the required properties of the final product.
- Tensioning System: The reinforcement materials are pulled under controlled tension to ensure that the fibers are properly aligned and uniformly distributed throughout the resin.
- Forming Guide: After the fibers are impregnated with resin, they are directed through a forming guide to ensure the fibers are properly positioned and compacted before entering the die.
- Die: The die shapes the impregnated fibers into the desired profile and holds them in place during the curing process. The die is typically heated to ensure that the resin cures and solidifies as the material passes through.
- Curing Oven: The die is usually followed by a heated oven where the resin hardens through a chemical reaction (curing process), which is essential for giving the part its final strength and rigidity.
b. Resin System
- Resin Tank: The resin tank stores the liquid resin that is used to impregnate the fiberglass reinforcements. This resin can be a thermosetting plastic, such as polyester or epoxy, which hardens permanently when heated.
- Metering Pump: The resin is pumped into the resin bath, ensuring a consistent flow rate that matches the speed of the pultrusion process.
- Additives and Fillers: Depending on the end product’s requirements, additional additives such as flame retardants, colorants, and fillers (e.g., calcium carbonate or silica) may be mixed with the resin.
c. Preform and Fiber Handling Equipment
- Fiber Spools: Continuous fibers (roving, mats, or tapes) are stored in large spools. These fibers are drawn from the spools and pulled through the resin bath.
- Tension Control: A tension control system ensures that the fibers are continuously pulled through the process at a constant speed and under controlled tension to maintain consistent fiber alignment and resin impregnation.
d. Cooling Section
- Cooling Zone: After the resin cures in the die, the part enters a cooling section where it is gradually cooled to room temperature to finalize the solidification process.
- Cooling Fans or Water Baths: Depending on the profile and resin used, parts may be cooled using fans, water baths, or other cooling methods to prevent thermal stresses or warping.
e. Cutter and Handling Systems
- Cutter: After the part exits the curing oven, it is cut to the required length by a cutting system. This is usually done with a high-speed rotating blade that provides precise cuts at specified intervals.
- Take-off System: The take-off system pulls the cured composite material out of the die and delivers it to the cutting station. This system is equipped with rollers or belts that handle the continuous pulling force and ensure consistent feed.
2. Pultrusion Process Flow
a. Resin Impregnation
- Fiberglass Feed: Continuous fiberglass reinforcement (roving, mats, or continuous strands) is unspooled and guided into the resin bath.
- Impregnation: The fibers are thoroughly soaked with resin as they pass through the resin bath, ensuring uniform resin content throughout the length of the fibers.
- Preform Formation: The resin-impregnated fibers are pulled through a forming guide, where the reinforcement material is arranged into the required shape for the part being produced.
b. Shaping and Curing in the Die
- The resin-impregnated fibers are pulled into a heated die, which determines the profile (shape) of the final part. The die can create a variety of profiles such as flat bars, angles, channels, beams, or rods.
- Curing: As the impregnated fibers travel through the heated die, the resin undergoes a chemical reaction (typically crosslinking) that cures and hardens the material, transforming it from a liquid to a solid state.
c. Cooling and Solidification
- After the part exits the heated die, it is cooled down to room temperature to solidify and stabilize the material. This cooling process is crucial to prevent any deformation or distortion of the part.
- The cooled composite part is then ready for cutting and handling.
d. Cutting and Finishing
- The continuous pultruded part is cut to the desired length using a saw or cutting machine, depending on the specifications of the final product.
- Quality Inspection: After cutting, the parts are inspected for defects such as voids, resin distribution issues, or dimensional errors. This ensures that only high-quality parts are shipped out.
3. Considerations for the Pultrusion Molding Area
a. Material Selection
- The choice of fiberglass reinforcement and resin significantly influences the properties of the final product. Common reinforcements include E-glass (for general use) and S-glass (for higher strength applications).
- The resin type (e.g., polyester, vinyl ester, or epoxy) must be chosen based on the required strength, chemical resistance, and environmental conditions in which the final product will be used.
b. Process Control
- Temperature Control: The temperature within the mold and curing die must be precisely controlled to ensure uniform curing of the resin and to prevent defects like incomplete curing, brittleness, or warping.
- Speed Control: The speed at which the material is pulled through the machine (typically 2-10 meters per minute) must be optimized to balance the rate of resin impregnation, curing time, and cooling rates.
- Resin Impregnation: Consistency in resin impregnation is crucial. Insufficient resin can lead to weak parts, while excessive resin may result in waste, part deformities, or slower curing times.
c. Cooling and Solidification
- Proper cooling is essential to prevent thermal stress and to ensure that the parts retain their shape and structural integrity after curing.
- Cooling rates should be optimized based on the material's thermal properties, with slower cooling required for thicker or larger profiles to avoid cracking or warping.
d. Equipment Maintenance
- Die Maintenance: The mold or die needs regular cleaning and maintenance to avoid resin buildup, which can cause defects or dimensional inaccuracies in the parts.
- Machine Calibration: The tensioning system, resin bath, and curing die must be calibrated and maintained regularly to ensure smooth operation and consistent part quality.
4. Safety and Environmental Considerations
a. Health and Safety
- Ventilation: The pultrusion molding area must be well-ventilated to remove fumes generated by the curing resin, especially if volatile organic compounds (VOCs) are released.
- Personal Protective Equipment (PPE): Operators should wear gloves, goggles, and respiratory protection to prevent exposure to resin fumes and fiberglass particles.
- Fire Prevention: Since resins can be flammable, fire extinguishers and safety protocols should be in place to handle potential resin spills or curing-related fires.
b. Waste Management
- Recycling: Some of the scrap material (such as excess resin or cut-off parts) can be recycled, but careful handling is required to separate contaminants from reusable material.
- Waste Disposal: Proper disposal methods for used resins, solvents, and other chemicals are necessary to prevent environmental contamination.